Textile promotional bags are one of the most popular ways to promote businesses.
They are durable, practical, and can be customized with various prints and logos. To achieve the highest quality and durability of prints, we use screen printing technology.
Screen printing is an industrial textile printing method that uses a fine mesh to transfer ink onto the material. This method is suitable for printing runs over 50 pieces and allows for the creation of high-resolution prints with saturated colors.
We use the highest quality inks and materials to ensure that our textile promotional bags will remain beautiful and high-quality for a long time.
What is screen printing on textiles?
Screen printing is a classic method for direct printing on textiles. With a vast variety of inks and application techniques, it can achieve stunningly effective images on various types of fabrics, both on finished products and on cut pieces. Modern technological lines can achieve excellent productivity, which is so important in mass production.
For us, screen printing is more than just a process of branding a piece of fabric. It is a complex process that requires close attention to the individual components involved to achieve a perfect end result. Screen printing is a creative process that requires attention to detail and creativity.
What is the screen printing process?

A screen stretched in a specific way is covered with a photosensitive emulsion that clogs the fine holes of the fabric.

Exposure
The design is printed on a transparent film, which is placed on the screen coated with photosensitive emulsion, and then exposed to light.

The areas of the emulsion that were protected by the transparent film are washed away, and the image of the design for printing is developed. The ink passes through the resulting image on the screen under a certain pressure and is applied to the textile.

Ink is applied to the screen (each color is on a separate screen), which is spread under pressure using a squeegee until the desired image is obtained.

To ensure the durability of the printed design, the garment is passed through a dryer set to a specific temperature for a specific time.
Screen printing inks and techniques
Water-based inks
Prints made with water-based inks are characterized by a soft feel and allow the fabric to remain breathable. When printed, the ink soaks into the fabric itself rather than remaining on the surface. These inks are the most environmentally friendly and meet all European quality, harmlessness and environmental requirements. One of the disadvantages of water-based inks is the difficulty in printing patterns with very fine details.
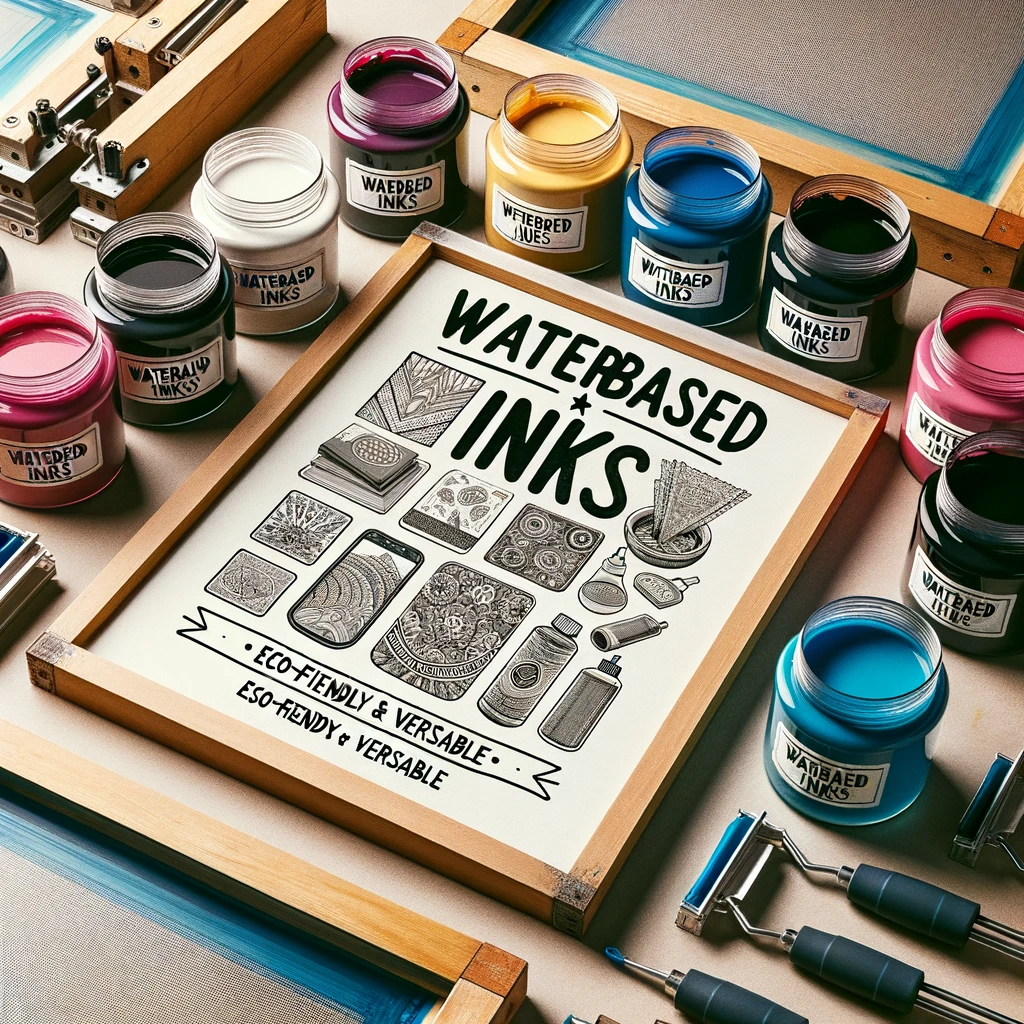
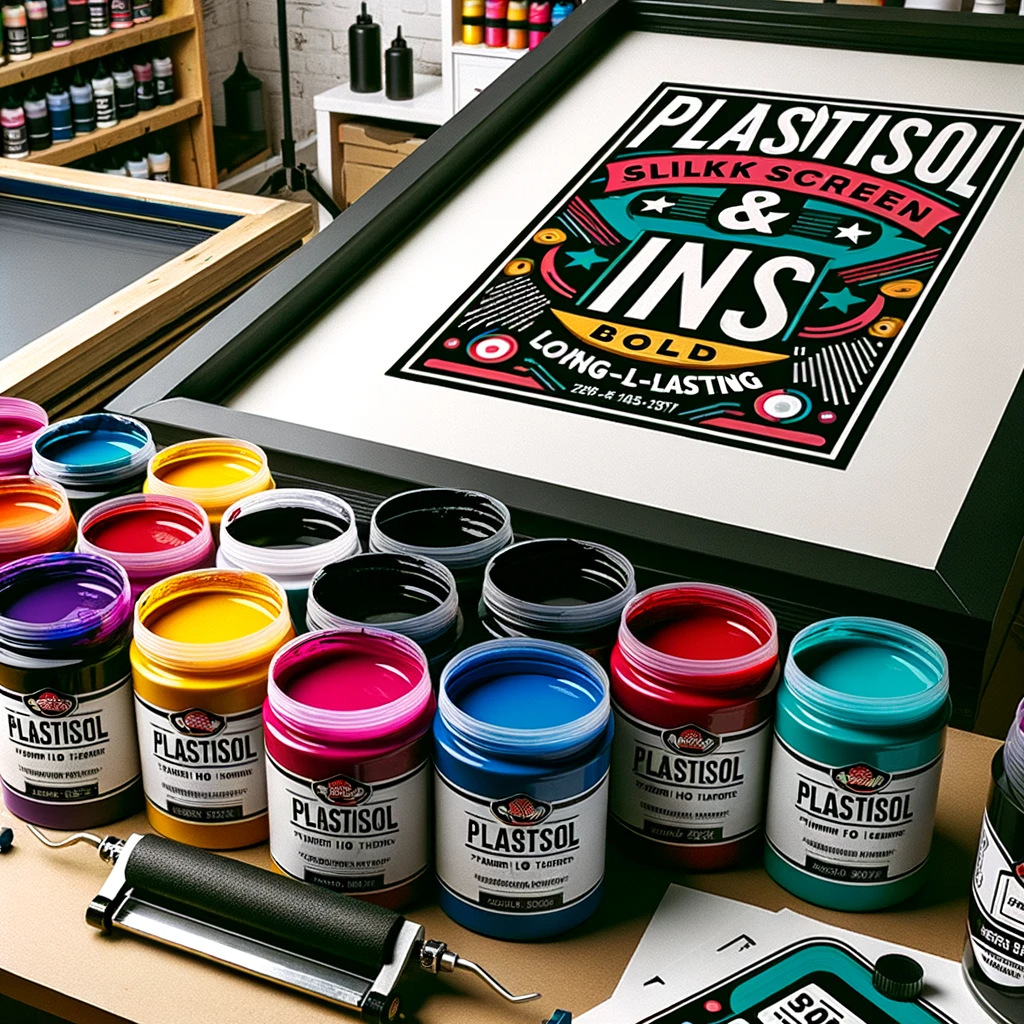
Plastisol inks
Plastisol inks are required for a large part of the prints. They achieve the brightest and most accurate colors, regardless of the material. When printed, plastisol inks remain on the surface itself, unlike water-based inks. They are felt to the touch and can also negatively affect the breathability of the garment. They can be used to print extremely fine details and can guarantee truly incredible printing results.
Discharge
Discharge printing technology uses water-based inks that decolorize dark fabrics, allowing for a soft hand feel and avoiding the printing of an additional underlay to achieve bright and realistic images. As a drawback, it should be noted that the fabric must be dyed in a specific way to achieve the desired result.
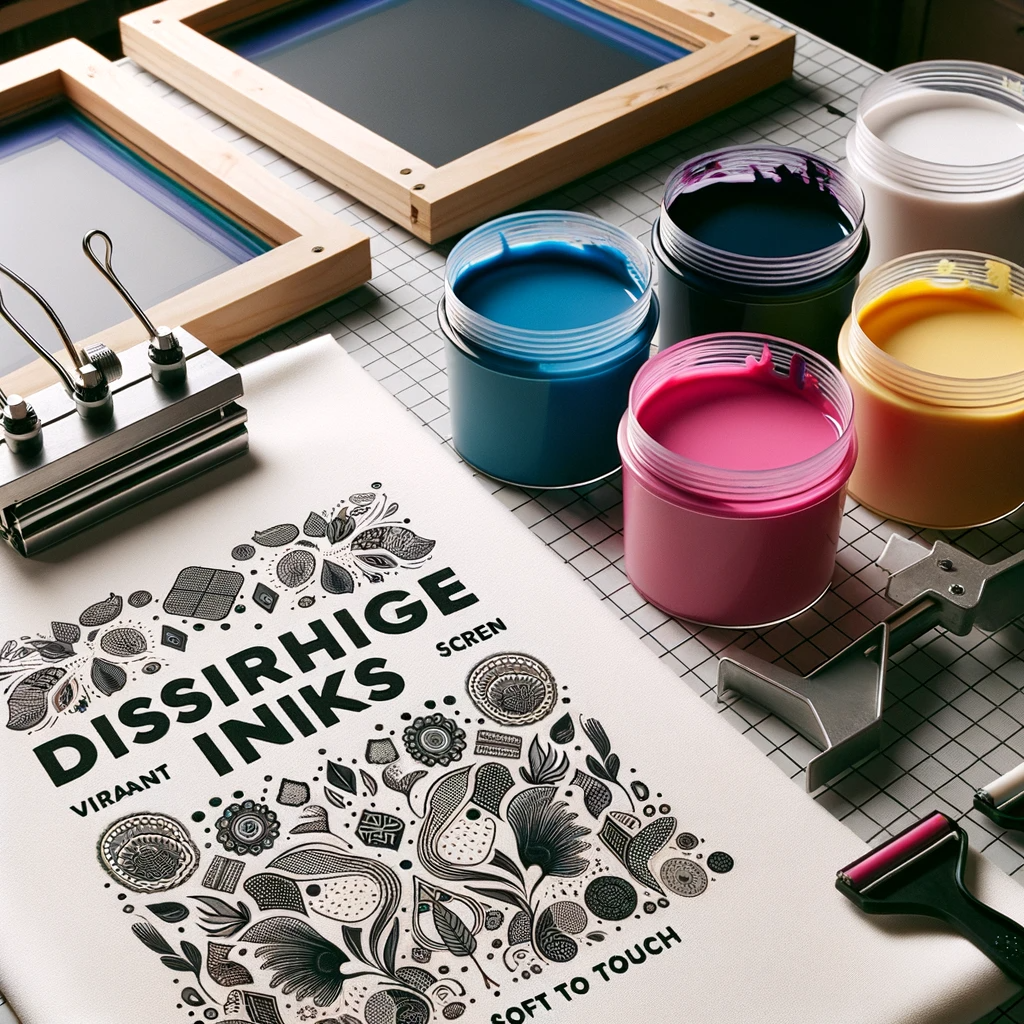
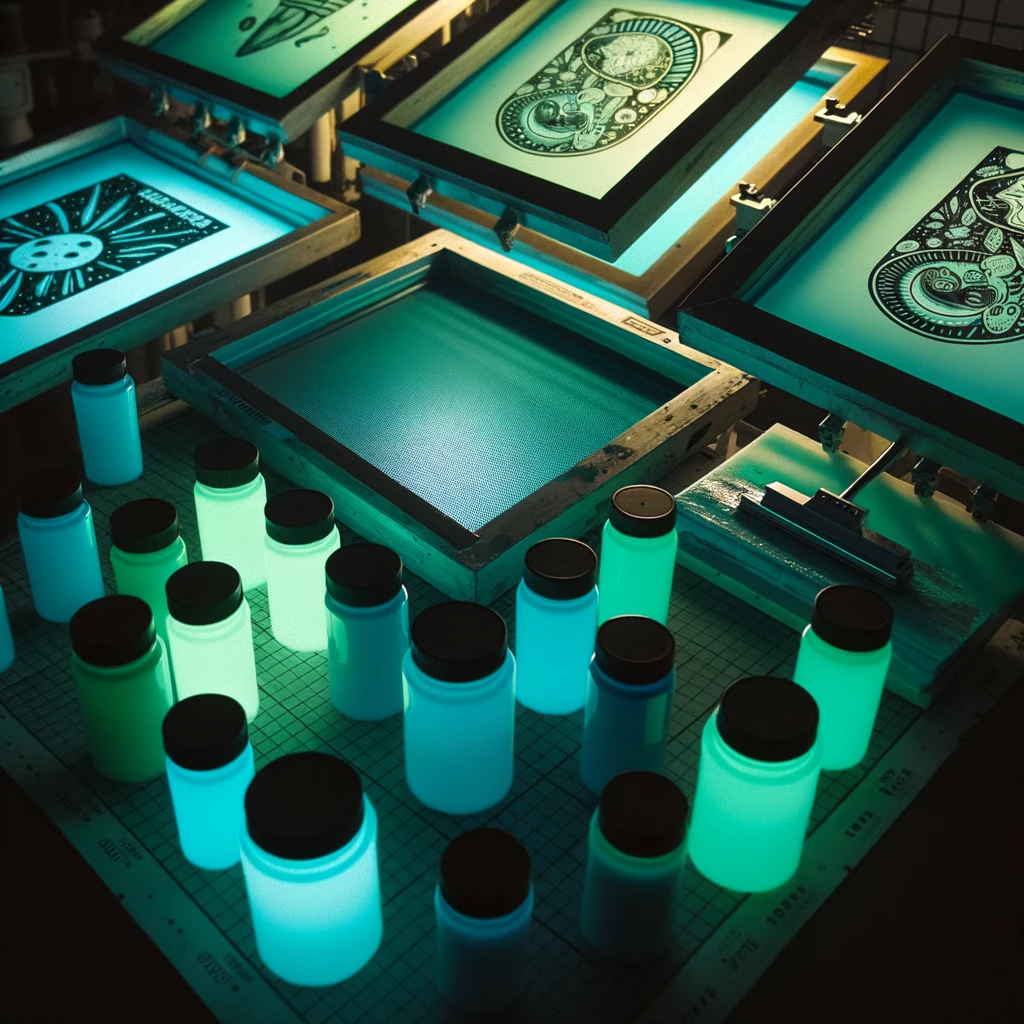
Phosphorescent inks
This type of ink allows your print to literally glow in the dark. In daylight, the print appears white, and in the dark, it glows green. When using this type of ink, the end result is truly unique. Some of the drawbacks include a coarser print detail and more ink build-up to achieve the desired effect.
CMYK (full color printing)
In this technique, the print colors are achieved by combining different values of the four primary colors CMYK (cyan, magenta, yellow, and black). This method is suitable for multi-color photorealistic prints for which Pantone colors cannot be defined. Among the disadvantages here is that the colors cannot be guaranteed as when working with Pantone colors.
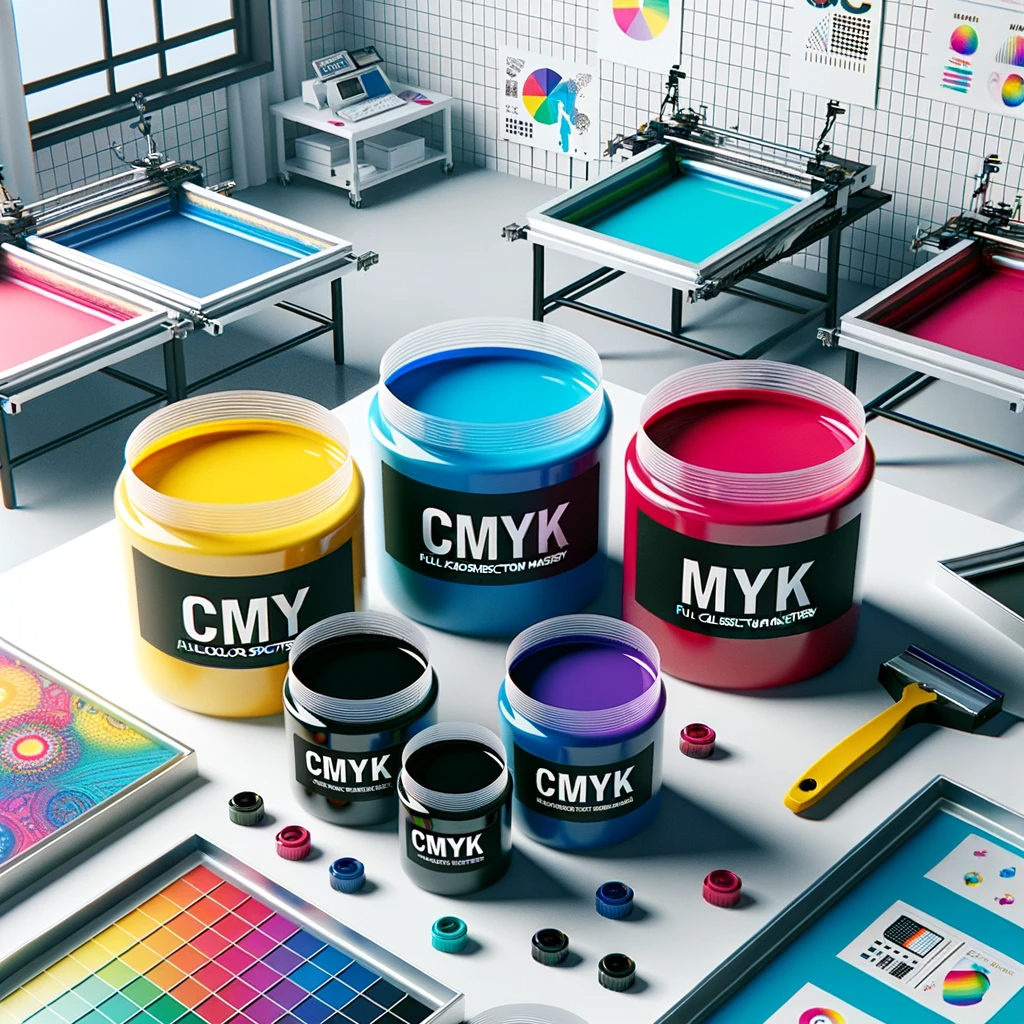
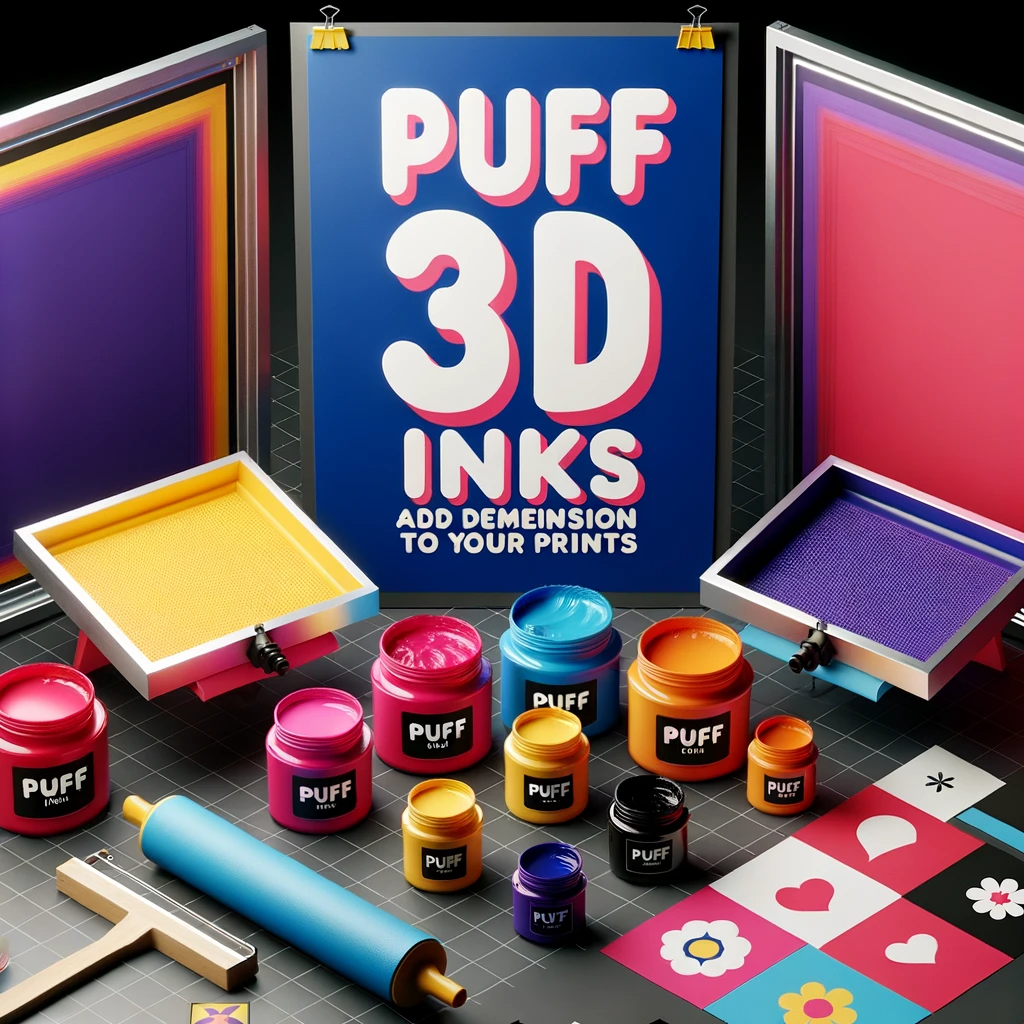
Puff (3D effect)
To create a 3D print, an inflating component is added to the inks, which allows the print itself to swell. This effect can be applied to both the entire print and individual elements of it. Disadvantages: difficult to achieve Pantone colors and low definition of the printed image.